Polyvinyl Alcohol (PVA) as a Textile Auxiliary Agent: Key Requirements in Warp Sizing and Stiffening Finishing
PVA serves critical roles in textile processing for warp sizing and stiffening finishes. For sizing, high-alcoholysis (≥99%), high-DP PVA (e.g., PVA-1799) strengthens cotton yarns, while partial-alcoholysis (~88%) variants suit synthetics. In stiffening, high-alcoholysis PVA provides permanent rigidity for heavy fabrics, and partial-alcoholysis types offer temporary stiffness for lightweight materials. Polymerization degree affects film strength (high DP) or flexibility (low DP). Optimal PVA selection by alcoholysis and DP balances weaving performance, fabric handle, and finishing durability, making it essential for efficient textile manufacturing.
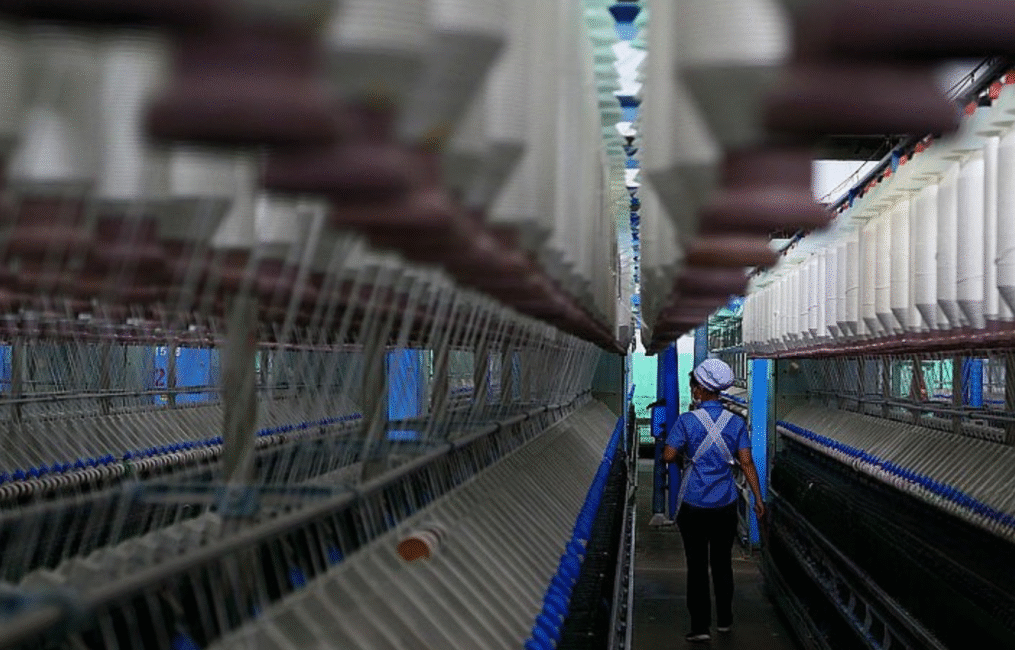
1. Introduction
Polyvinyl Alcohol (PVA) is a widely used water-soluble polymer in textile processing, particularly in warp sizing and stiffening finishing. Its performance in these applications depends heavily on two critical parameters:
- Alcoholysis Degree (AD): The percentage of hydroxyl (–OH) groups replacing acetate groups in the PVA chain.
- Polymerization Degree (DP): The average number of repeating monomer units in the PVA molecule.
This article explores the specific requirements for PVA in warp sizing and stiffening finishing, along with the optimal alcoholysis degree and polymerization degree for each application.
2. PVA in Warp Sizing
2.1 Key Requirements for Warp Sizing
Warp sizing aims to:
- Enhance yarn strength to withstand weaving tension.
- Reduce yarn hairiness to minimize breakage.
- Improve abrasion resistance for high-speed looms.
- Ensure easy desizing (removal after weaving).
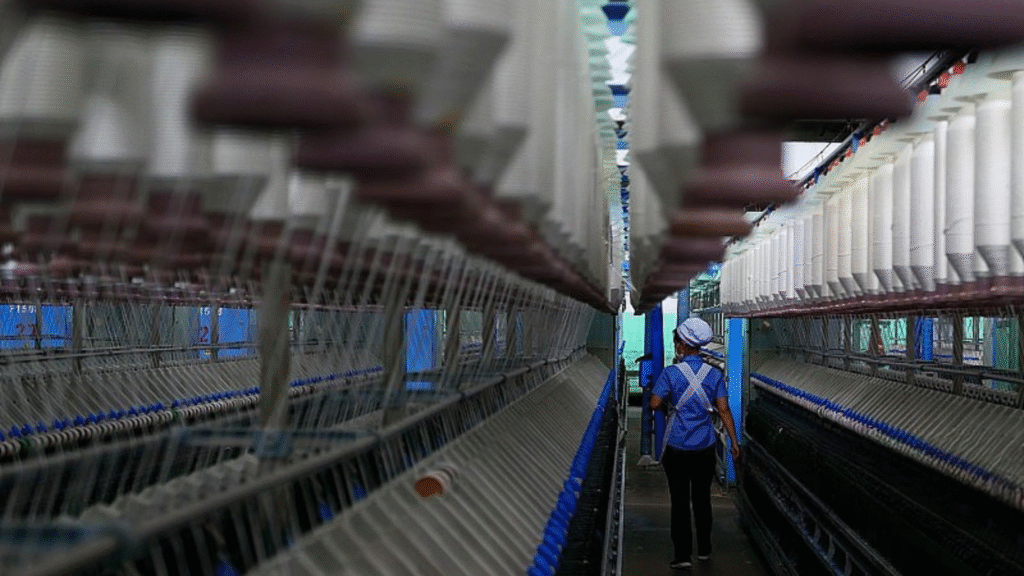
2.2 Optimal PVA Specifications for Sizing
Parameter | High Alcoholysis (≥99%) | Partial Alcoholysis (~88%) |
---|---|---|
Solubility | Hot water (>85°C) | Cold or warm water (~60°C) |
Film Strength | High (rigid film) | Moderate (flexible film) |
Adhesion | Best for cotton, viscose | Better for synthetics (polyester, nylon) |
Desizing Difficulty | Harder (needs hot water/enzymes) | Easier (cold water soluble) |
Polymerization Degree (DP) Selection
- High DP (1700-2500, e.g., PVA-1799):
- Provides superior film strength, ideal for high-speed weaving (e.g., denim, canvas).
- Higher viscosity requires higher temperature dissolution.
- Medium DP (1000-1700, e.g., PVA-1788):
- Balanced penetration and film strength, suitable for cotton-polyester blends.
- Low DP (500-1000, e.g., PVA-0588):
- Easy dissolution, good for fine yarns (e.g., voile, shirting fabrics).
Recommended PVA Grades for Sizing
- 100% Cotton (High-Density Weaving): PVA-1799 (99% AD, DP 1700-1800).
- Polyester-Cotton Blends (T/C): PVA-1788 (88% AD, DP 1700-1800).
- Pure Synthetic Fibers (Polyester/Nylon): PVA-0588 (88% AD, DP 500-600).
3. PVA in Stiffening Finishing
3.1 Key Requirements for Stiffening
Stiffening agents must:
- Provide temporary or permanent stiffness depending on fabric end-use.
- Maintain flexibility to avoid brittleness.
- Be compatible with other finishing chemicals (e.g., softeners, resins).
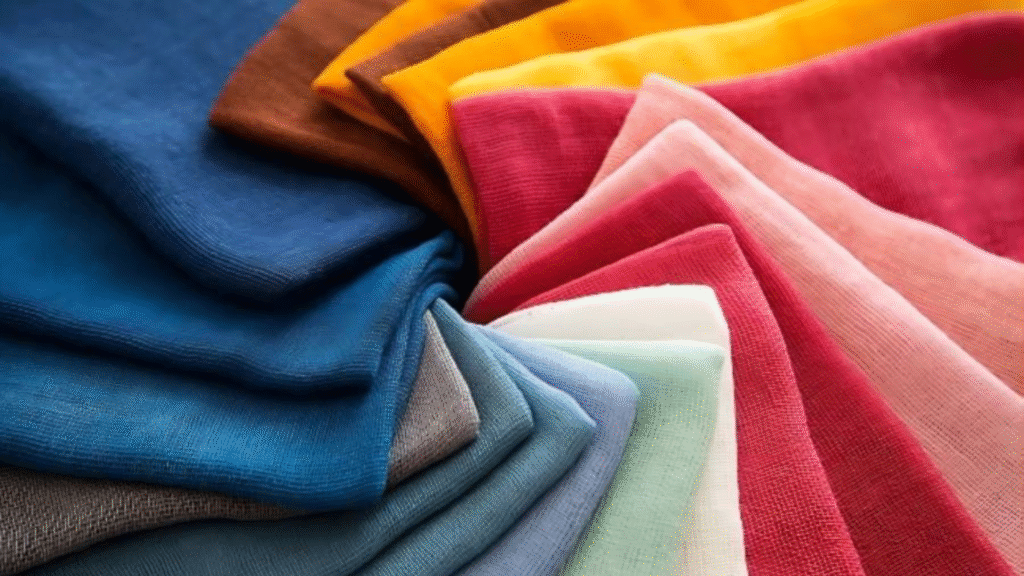
3.2 Optimal PVA Specifications for Stiffening
Parameter | High Alcoholysis (≥99%) | Partial Alcoholysis (~88%) |
---|---|---|
Stiffness Level | High (crisp handle) | Moderate (softer handle) |
Water Resistance | Excellent (heat-treated) | Poor (dissolves in water) |
Durability | Long-lasting | Temporary (wash-off easily) |
Polymerization Degree (DP) Selection
- High DP (1700-2500):
- Maximum stiffness, used in heavy fabrics (e.g., canvas, upholstery).
- Medium DP (1000-1700):
- Balanced stiffness & flexibility, for apparel fabrics (e.g., shirt collars).
- Low DP (500-1000):
- Soft stiffening, for lightweight fabrics (e.g., linings, embroidery backing).
Recommended PVA Grades for Stiffening
- Permanent Stiffness (e.g., formalwear, industrial fabrics): PVA-1799 (99% AD, high DP).
- Semi-Durable Stiffness (e.g., dress shirts): PVA-1788 (88% AD, medium DP).
- Temporary Stiffness (e.g., embroidery stabilizers): PVA-0588 (88% AD, low DP).
4. Conclusion
- Warp Sizing:
- High-alcoholysis (99%) + high-DP PVA for cotton & high-speed weaving.
- Partial-alcoholysis (88%) + low-DP PVA for synthetics & easy desizing.
- Stiffening Finishing:
- High-alcoholysis PVA for permanent stiffness (e.g., suiting fabrics).
- Partial-alcoholysis PVA for temporary or flexible stiffening (e.g., lightweight textiles).
By selecting the right alcoholysis degree and polymerization degree, textile manufacturers can optimize weaving efficiency, fabric hand feel, and finishing durability.