Abstract
Powder coatings have excellent environmental properties and superior coating effects. This article introduces how to select suitable titanium dioxide pigments for powder coatings, suggesting consideration of the following properties of titanium dioxide:
- Type of titanium dioxide;
- Surface treatment of titanium dioxide;
- Particle size distribution of titanium dioxide;
- pH value of titanium dioxide;
- Moisture content of titanium dioxide.
Introduction
Powder coatings, as a representative of solvent-free, high-solid-content coatings, have significantly lower volatile organic compound (VOC) emissions compared to traditional solvent-based coatings, with some products achieving zero VOC emissions.
Powder coatings are composed of polymers such as polyester resin, polyurethane, polyacrylic acid, and epoxy resin, uniformly mixed with pigments and additives. Powder coatings are easy to apply, often requiring only one coat to meet usage requirements. With good process control, the coating film is generally free of pores and has excellent acid and alkali resistance, as well as corrosion resistance.
Industries that primarily use powder coatings include furniture manufacturing, home appliance and kitchenware manufacturing, steel pipe industry, automotive industry, agricultural machinery industry, fire equipment, electrical industry, and construction industry.
Properties of Titanium Dioxide
The main component of titanium dioxide is TiO2, which is currently the most effective white pigment. Due to its high refractive index, titanium dioxide has better light-scattering ability than other white pigments, providing excellent coverage in coating applications.
The refractive indices of common white pigments are shown in Table 1. Titanium dioxide-based coatings function to cover, beautify, and protect substrates, preventing rust and corrosion caused by light, heat, and moisture. In summary, the basic functions of titanium dioxide in the industry are “covering, beautifying, and protecting.”
Substance | Refractive Index | Substance | Refractive Index |
---|---|---|---|
Rutile Titanium Dioxide | 2.71 | Basic Lead Carbonate | 2.00 |
Anatase Titanium Dioxide | 2.52 | Basic Lead Sulfate | 1.93 |
Zinc Sulfide | 2.37 | Barium Sulfate | 1.64 |
Zinc Oxide | 2.02 | Talc | 1.87 |
Table 1: Refractive Indices of Common White Pigments
The Important Role of Titanium Dioxide in Powder Coatings
In the formulation design of powder coatings, the combination of resin and crosslinker is often considered the primary factor affecting performance, leading to significant efforts in resin and crosslinker development. However, this does not mean that titanium dioxide is less important or can be arbitrarily adjusted. Titanium dioxide significantly impacts the production, application, and film properties of powder coatings.
During production, the dispersibility of titanium dioxide directly affects the mixing efficiency and the dispersion of the melt during extrusion, as well as production capacity. During the curing process, the surface properties of titanium dioxide influence the flowability of the melt, curing speed, and yellowing during over-baking.
In terms of film performance, titanium dioxide affects the coverage, gloss, and weather resistance of the coating. Therefore, selecting the appropriate titanium dioxide is crucial in developing powder coatings.
When selecting titanium dioxide, consider the following properties:
- Type of titanium dioxide;
- Surface treatment of titanium dioxide;
- Particle size distribution of titanium dioxide;
- pH value of titanium dioxide;
- Moisture content of titanium dioxide.
(1) Type of Titanium Dioxide
Commercial titanium dioxide can be divided into two main types: anatase and rutile. The crystal characteristics and physical constants of titanium dioxide are shown in Table 2.
Due to differences in chemical structure, although both are titanium dioxide, their performance varies. Coatings made with anatase titanium dioxide are prone to chalking under sunlight, while those made with rutile titanium dioxide have better anti-chalking properties. Therefore, rutile titanium dioxide is recommended.
Property | Rutile | Anatase |
---|---|---|
Crystal System | Tetragonal | Tetragonal |
Crystal Shape | Needle-like | Cone-like |
d(μm) | 0.2-0.5 | 0.1-0.5 |
Relative Density | 4.2-4.3 | 3.8-3.9 |
Refractive Index | 2.71 | 2.52 |
Mohs Hardness | 6-7 | 5.5-6 |
Melting Point | 1858℃ | Transforms to Rutile |
Specific Heat Cal/℃.g | 0.17 | 0.17 |
UV Absorption Rate% | 90 | 67 |
Coverage m2 /kg | 30.1 | 23.6 |
Tinting Strength(Reynolds) | 1650 | 1270 |
Lattice Constant | α=0.459 | α=0.378 |
c=0.296 | c=0.95 |
Table 2: Crystal Characteristics and Physical Constants of Titanium Dioxide
(2) Surface Treatment of Titanium Dioxide
To enable titanium dioxide to perform specific functions in different powder coating systems, various surface treatments are applied during production. For example, hydrated alumina (aluminum hydroxide) is used to improve dispersibility and gloss, while hydrated silica and hydrated zirconia are used to enhance weather resistance.
Organic surface treatments such as polyols, amines, or silanes are used to improve wetting and flowability. The whiteness of titanium dioxide depends on the TiO2 content; higher levels of surface treatment agents reduce the TiO2 content, affecting whiteness. Therefore, for higher whiteness in coatings, titanium dioxide with lower levels of surface treatment agents is preferred.
The gloss of the coating film depends not only on the resin and formulation but also on the surface treatment of titanium dioxide. Alumina surface treatment helps disperse titanium dioxide in the resin system, enhancing optical properties such as gloss and coverage. The crystallinity of alumina also contributes to gloss improvement.
For semi-gloss or matte coatings, titanium dioxide with silica surface treatment can be selected. Commercial titanium dioxide often has both alumina and silica surface treatments, categorized into high-gloss, gloss, and matte types based on functionality.
Silica surface treatment can be either loosely adsorbed or precipitated. Loosely adsorbed treatment results in a fluffy surface structure, larger particle size, increased effective surface area, and higher oil absorption. This structure helps improve dry film coverage by avoiding excessive crowding and spatial effects.
Precipitated treatment involves tightly wrapping silica around TiO2 particles, like a chocolate coating. This tight structure reduces the interaction between active titanium ions on the TiO2 surface and external polymers, preventing yellowing, fading, or chalking.
Thus, titanium dioxide can be categorized into outdoor high-weather resistance and indoor types based on weather resistance, with different applications shown in TEM images in Figure 1.
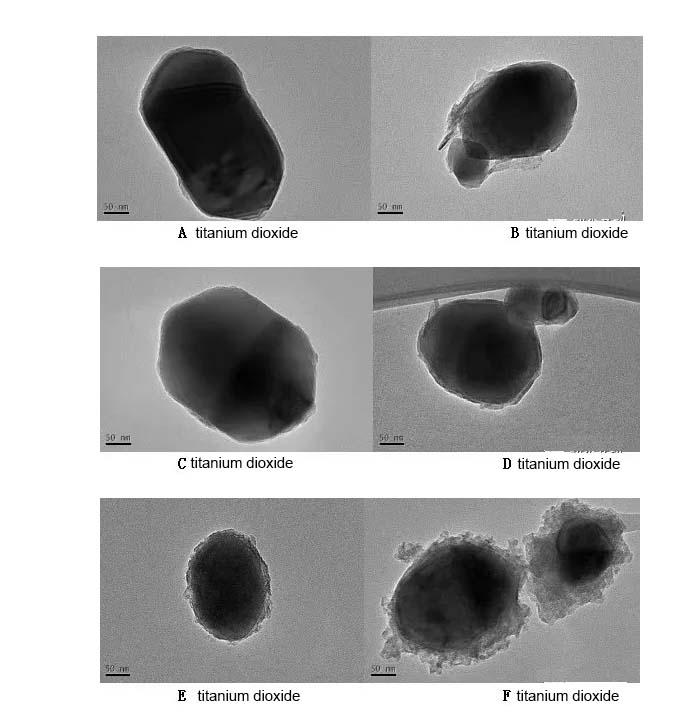
The properties of titanium dioxide can be distinguished by surface treatment, but detailed chemical and structural characteristics require discussion with technical personnel to select the appropriate titanium dioxide for product design.
(3) Particle Size Distribution of Titanium Dioxide
The particle size of titanium dioxide determines the color tone of the coating film. To achieve optimal optical performance, titanium dioxide is typically manufactured with a particle size around 0.2 microns, with a distribution curve from 0.15 to 0.3 microns.
Smaller particles scatter more blue light, resulting in a “blue-white” hue, while larger particles tend towards a “yellow-white” hue. The relationship between particle size and scattering power is shown in Figure 2. However, yellowing in titanium dioxide powder can occur due to residual vanadium or iron ions from incomplete purification during manufacturing.
Therefore, when specifying a particular color tone in powder coatings, attention should be paid to the particle size and distribution of titanium dioxide. In addition to dispersibility, particle size also affects coverage, as shown in Figure 3.

(4) pH Value of Titanium Dioxide
The pH value of titanium dioxide generally has a more significant impact on water-based coatings, affecting the performance of dispersants and thickeners. In powder coatings, the pH value should be considered based on the free acid concentration in the resin or the type of accelerator used.
In acid-catalyzed processes, titanium dioxide with a high pH can neutralize the catalyst, leading to incomplete curing and reduced film hardness. Titanium dioxide with a low pH can accelerate acid catalysis, causing over-curing and surface defects. A pH value of 7-8 is generally recommended.
(5) Moisture Content of Titanium Dioxide
Titanium dioxide powder can adsorb moisture from the environment, increasing its moisture content. Higher moisture content can lead to poor dispersion, reduced flowability, clogging of pipelines, and surface defects such as wrinkles, pinholes, and fish eyes in the coating film.
The extent of moisture adsorption is related to the concentration of surface treatment agents; generally, higher levels of treatment agents increase moisture adsorption. Therefore, it is essential to control the temperature and humidity of the storage environment. The recommended warehouse temperature is below 27°C, with relative humidity not exceeding 75%. To prevent “powder dust storms,” ventilation should be enhanced to maintain air circulation and reduce indoor dust concentration.
The moisture content of powders, including titanium dioxide and fillers, should not exceed 0.5%.
4. Evaluation Methods for the Suitability of Titanium Dioxide in Powder Coatings
Like other raw materials, titanium dioxide cannot meet all design requirements. It may excel in certain properties while having negative effects in others. Therefore, product characteristics must be considered when selecting titanium dioxide.
The evaluation of titanium dioxide suitability is typically divided into three main properties:
- Powder properties: fineness distribution, powder flowability, and gelation activity.
- Coating optical performance: color, coverage, gloss (20°, 60°), and yellowing during over-baking.
- Coating mechanical properties: hardness, solvent resistance, flexibility, and impact resistance.
5. Conclusion
In powder coating formulation design, adjustments are often made based on different requirements. The basic formulation typically includes resin, crosslinker, pigment, filler, and other additives. Titanium dioxide is an essential component of powder coatings.
This article aims to provide another perspective for research and development in the coatings and titanium dioxide industries. It offers reference value for the production of titanium dioxide, the development of new titanium dioxide products, and the application of titanium dioxide in powder coatings.