Carbon Black in Rubber: Properties, Applications & Key Grades (N110, N220, N330, N550, N660)
Carbon black is a fine black powder composed primarily of elemental carbon in the form of finely divided particles. Produced through the incomplete combustion or thermal decomposition of hydrocarbons under controlled conditions, carbon black is widely used as a reinforcing filler in rubber products—especially in the manufacture of tires. The performance of rubber products heavily
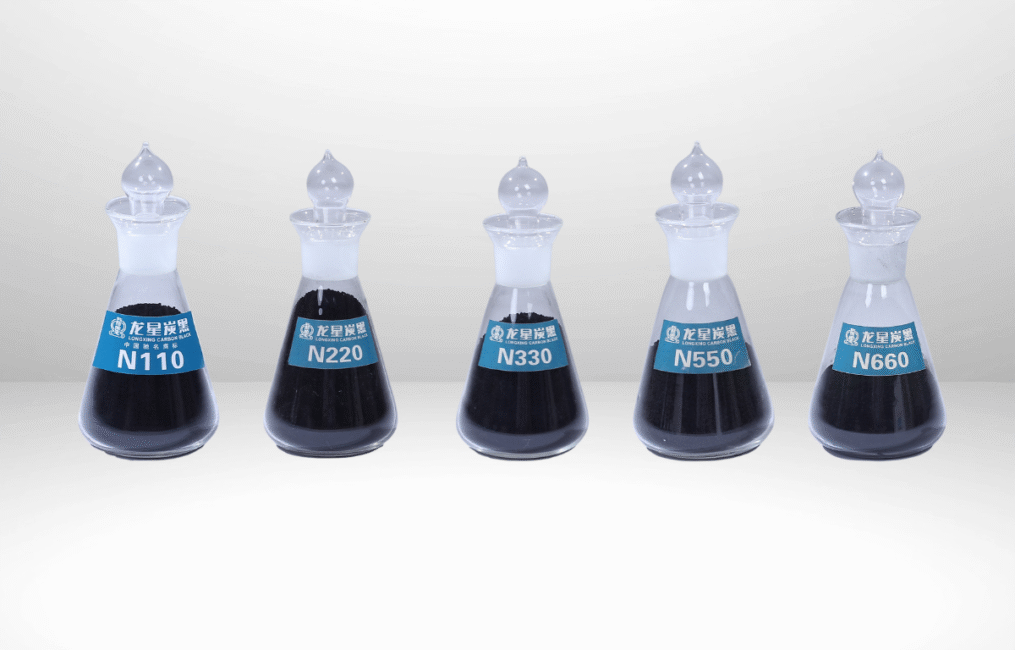
Carbon black is a fine black powder composed primarily of elemental carbon in the form of finely divided particles. Produced through the incomplete combustion or thermal decomposition of hydrocarbons under controlled conditions, carbon black is widely used as a reinforcing filler in rubber products—especially in the manufacture of tires. The performance of rubber products heavily depends on the grade and characteristics of the carbon black used.
This article introduces the key properties of various carbon black grades and focuses on the commonly used types in rubber applications—N110, N220, N330, N550, and N660.
1. Key Properties of Carbon Black
Carbon black grades are primarily distinguished by properties such as surface area, structure, oil absorption, and performance in rubber compounds. These parameters affect processing, reinforcement, elasticity, conductivity, and wear resistance. Below is a summarized comparison table of commonly used carbon black grades in rubber.
Carbon Black Grade Property Index
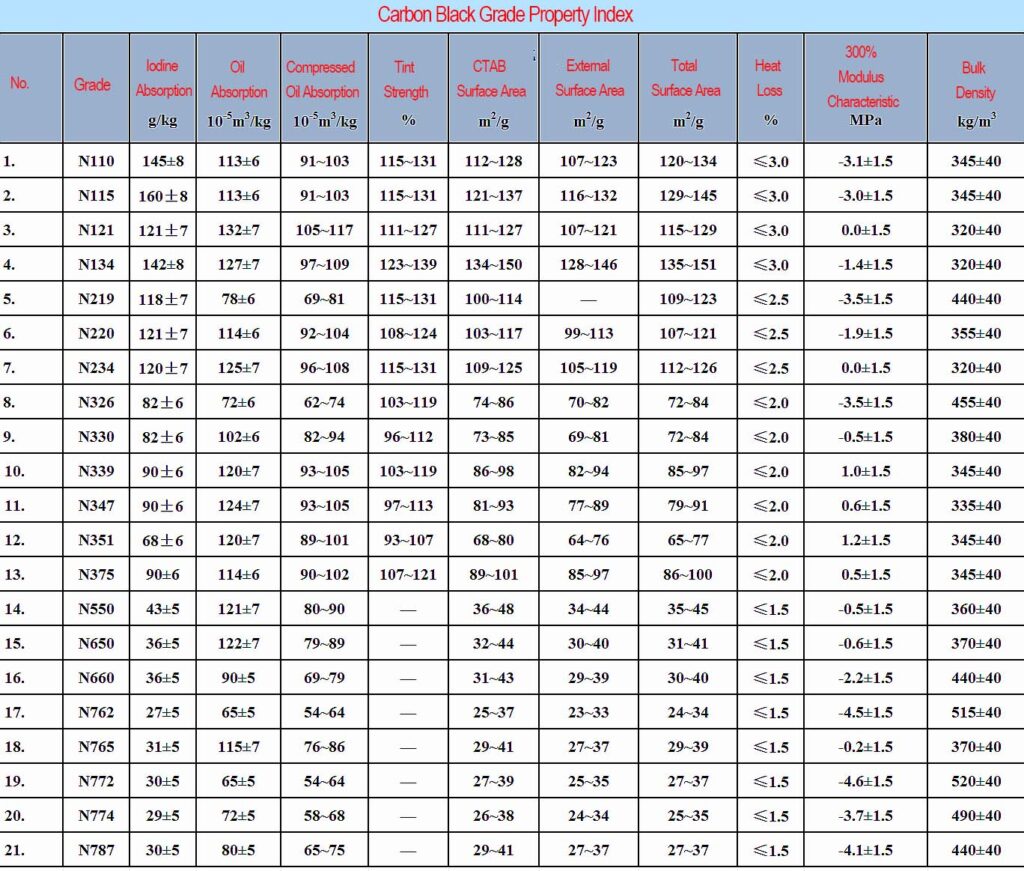
These values reflect each grade’s surface characteristics and reinforcing potential. Higher surface areas (such as with N110) usually mean stronger reinforcement, but also more challenges in processing.
2. Application and Performance of Key Rubber-Grade Carbon Blacks
To guide compound formulation and product design, understanding the performance and application of each carbon black grade is crucial.
Detailed Comparison of Major Rubber Carbon Black Grades
Grade | Application | Usage and Effect |
---|---|---|
N110 | Mainly used for off-road tires, heavy-duty tire treads, bridge rubber pads, conveyor belts, and other rubber products requiring excellent wear resistance. | N110 is one of the finest particle size grades among rubber carbon blacks, offering high reinforcement and good wear resistance. However, it has poor processing performance (high mixing energy consumption, difficult dispersion, poor calendering and extrusion), which limits its applications. It is often used in combination with N220 and N330. |
N220 | Used in heavy-duty and passenger car tire treads, as well as high-strength, high-wear-resistant rubber products like strong conveyor belts and industrial rubber parts. | Suitable for various rubbers. Compared with N330, rubber compounds with N220 have 10%–20% better wear resistance, higher tensile strength, and tear resistance, with some conductivity. However, it has higher heat buildup and hardness. |
N330 | Applied to passenger and truck tire treads, conveyor belt covers, hoses, and other industrial rubber products requiring high abrasion resistance. | Provides reinforcement, wear resistance, and crack growth resistance similar to N220. It also has good extrusion performance, especially suitable for SBR/BR blends. However, tread compounds with N330 have relatively higher rolling resistance among the N300 series, which should be considered during formulation. |
N550 | Used in tire carcass plies, sidewalls, inner tubes, as well as extrusion and calendering compound materials. | Suitable for natural and various synthetic rubbers. It disperses easily and provides good stiffness, fast extrusion speed, small die swell, and smooth surface. Vulcanizates have good high-temperature and thermal conductivity properties. Reinforcement, elasticity, and resilience are also good. When used in butyl rubber inner tubes, it is often combined with N660. |
N660 | Used in tire carcass plies, inner tubes, bicycle tires, hoses, belts, cables, footwear, calendered products, molded goods, etc. | Suitable for all types of rubber. Compared to semi-reinforcing furnace black, N660 has higher structure and finer particles. It disperses easily and provides vulcanizates with higher tensile strength, tear resistance, and modulus, while maintaining low deformation, low heat buildup, and good elasticity and flex resistance. However, its elongation is relatively low. |
3. Selecting the Right Carbon Black for Rubber Applications
Choosing the right carbon black depends on the desired balance between reinforcement, processability, rolling resistance, and cost. For instance:
- N110 is ideal for maximum reinforcement but is harder to process.
- N220 offers high wear resistance and strength with better processability.
- N330 balances performance and cost for general-purpose tires.
- N550 and N660 are better for flexibility, extrusion, and sidewall compounds.
Conclusion
Carbon black plays a vital role in the performance of rubber products. Each grade brings distinct mechanical and processing characteristics that influence the final properties of the compound. Understanding the Carbon Black Grade Property Index alongside the application performance of each grade enables formulators and manufacturers to optimize rubber compounds for their specific needs.